AI is supercharging robotics in manufacturing, making factories smarter and more efficient. It cuts labor costs by automating repetitive tasks and boosts safety by reducing manual labor risks—no more “watch your step” signs. Predictive maintenance keeps machines humming smoothly, cutting downtime by 15%. Quality control? AI nails it with 90% defect detection accuracy, ensuring high-quality products. Real-time optimization slashes lead times, and continuous ops mean no coffee breaks for bots. With the AI and robotics market set to explode, the future of manufacturing is not just bright; it’s dazzling. Stick around to find out how these technologies will shape tomorrow’s factories!
Table of Contents
Key Takeaways
- AI-driven predictive maintenance reduces unplanned downtime by 15%, enhancing efficiency.
- Real-time AI optimization minimizes production bottlenecks, boosting overall productivity.
- AI algorithms improve defect detection accuracy up to 90%, increasing quality control.
- Automation with AI lowers labor costs and operational errors, streamlining processes.
- AI integration in robotics enhances safety, reducing workplace accidents by 50%.
Enhanced Worker Safety
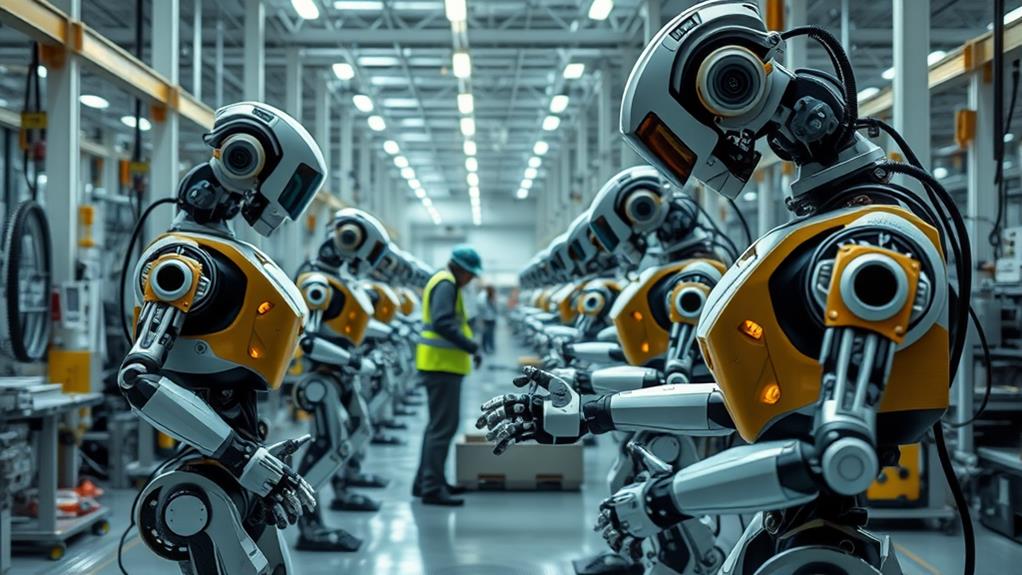
By integrating AI with robotics in manufacturing, companies are greatly enhancing worker safety. Imagine a factory where robots handle the heavy lifting and precise assembly tasks, while humans monitor from a safe distance. Advanced robotics equipped with AI capabilities make this vision a reality, reducing the risk of injuries associated with manual labor.
AI-driven safety systems are the unsung heroes here, constantly processing real-time data from sensors to guarantee operations within safe parameters. If any unsafe conditions arise, immediate alerts are sent to workers, keeping everyone out of harm’s way. It’s like having a vigilant guardian angel watching over every move.
Moreover, predictive maintenance powered by AI identifies potential equipment failures before they occur, preventing accidents linked to malfunctioning machinery. This technology is not just about fixing things before they break; it’s about creating a safer, more efficient work environment.
Studies reveal up to a 50% reduction in workplace accidents where AI and robotics are implemented. This statistic isn’t just a number—it’s a verification of the transformative power of automation.
Cost Reduction Strategies
Cost reduction strategies in manufacturing are increasingly centered around the integration of AI and robotics. Imagine this: intelligent machines working tirelessly to streamline operations, while you sip your coffee and marvel at the efficiency. By automating repetitive tasks, robotics can considerably lower labor costs.
The human workforce, then, isn’t just twiddling their thumbs—they’re redirected to higher-value roles, boosting productivity without inflating expenditures.
But wait, there’s more! AI-driven predictive maintenance can slash maintenance costs by 18%-25% and bolster production line availability by a solid 15%. This isn’t just about saving a few pennies; it’s about smart resource allocation. And who wouldn’t want to optimize that?
Automation also brings a treasure trove of operational cost savings. Think fewer errors and streamlined processes, which translate to a higher ROI.
Plus, advanced robotics systems can operate non-stop, reducing the cost per unit produced.
And let’s not forget inventory management. With AI, you can minimize excess stock and cut down those pesky carrying costs. Efficient, right?
In the grand scheme of manufacturing, AI and robotics aren’t just a luxury—they’re a game-changing necessity.
Predictive Maintenance
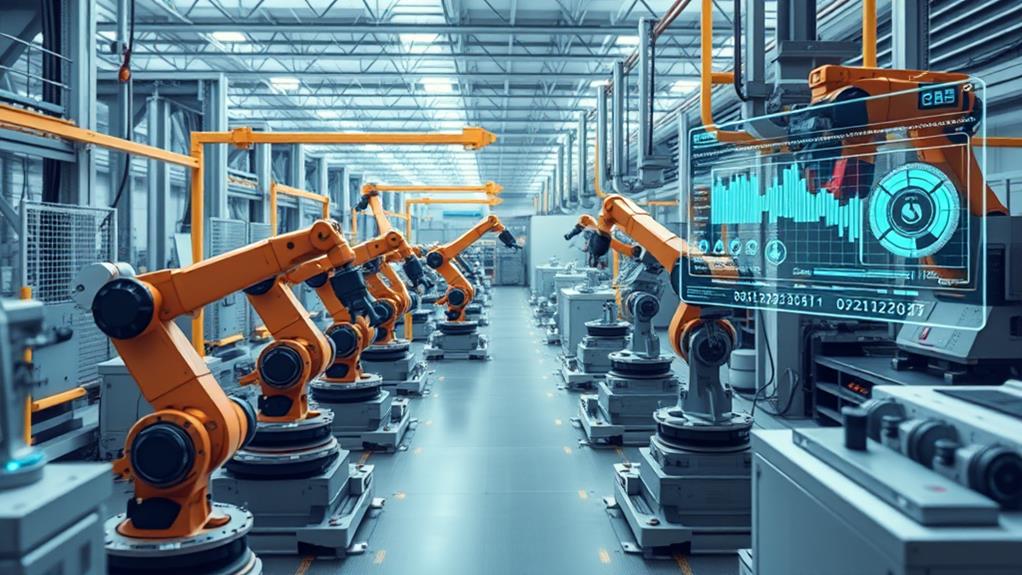
Predictive maintenance represents a notable leap forward in manufacturing efficiency, leveraging AI to anticipate and address potential equipment failures before they occur. This proactive approach is revolutionizing maintenance by integrating robots and AI systems with predictive analytics to monitor and analyze real-time data.
IoT sensors play a pivotal role, gathering vital information on machine performance, including parameters like temperature, vibration, and lubrication.
By shifting to predictive maintenance, manufacturers can considerably reduce unplanned downtime, which has historically wreaked havoc on operational efficiency and productivity. Imagine a production line that never stops unexpectedly; that’s the power of predictive maintenance. This technology can improve production line availability by up to 15%, enhancing overall efficiency. It’s like having a crystal ball but way cooler and more practical.
Moreover, AI-driven predictive maintenance can lower maintenance costs by 18%-25%, offering substantial savings and better resource management within manufacturing processes.
Fundamentally, you’re not just fixing problems; you’re preventing them. With predictive maintenance, factories can optimize their operations, ensuring that robots and machinery work seamlessly, transforming the manufacturing landscape into a well-oiled machine—literally and figuratively.
Quality Control Innovations
As manufacturers harness the power of predictive maintenance to bolster operational efficiency, they are also revolutionizing quality control through AI-driven innovations. Imagine a world where mistakes are almost a thing of the past—that’s the promise AI brings to quality control.
Manufacturing companies are now leveraging sophisticated AI algorithms and advanced computer vision technologies to scrutinize production lines with eagle-eyed precision. This high-tech marvel guarantees that defects are detected with a jaw-dropping accuracy rate of up to 90%, far beyond what traditional methods could ever dream of achieving.
But it doesn’t stop there. Predictive maintenance powered by AI slashes downtime and maintenance costs by up to 40%, meaning equipment runs smoothly, and production quality soars. The integration of AI allows for nimble adjustments in manufacturing workflows, cutting lead times by a remarkable 25%.
Enter collaborative robots (cobots), working hand-in-hand with human operators to make these rapid changes possible. The result? A notable boost in customer satisfaction, with repeat business climbing by 10-15%.
In this brave new world of manufacturing, the synergy between AI and robotics systems is not just boosting efficiency—it’s setting new standards for quality control.
Real-Time Optimization

Seamlessly integrating AI algorithms, real-time optimization in manufacturing automation is revolutionizing the industry. Imagine a factory where production schedules and workflows are adjusted instantly, thanks to AI in manufacturing. This isn’t a far-off dream but a reality enhancing efficiency by up to 20%.
By continuously monitoring equipment, AI-driven systems enable predictive maintenance, reducing downtime by 15% and extending machinery life. Who wouldn’t want that?
Adaptive production processes are another game-changer. When AI and robotics join forces, robots modify tasks based on real-time data, increasing flexibility and slashing waste. This dynamic duo not only streamlines operations but also boosts production output, with some companies enjoying up to a 30% improvement.
Moreover, real-time optimization lets manufacturers respond to market demands faster, cutting lead times by as much as 25%. Production constraints? Not a problem. With sophisticated manufacturing software, bottlenecks dissolve, and productivity surges.
Future Trends and Projections
The future of AI and robotics in manufacturing is poised for substantial growth and transformation. Imagine factories where machines not only perform tasks but also predict and adapt to changes even before they happen.
AI is set to revolutionize how we think about efficiency and automation, with projections indicating a whopping $182 billion market by 2027. That’s not just a number; it’s a showcase of the transformative power of these technologies.
By 2030, AI in manufacturing will skyrocket from $2.3 billion in 2022 to an impressive $23.6 billion. This surge reflects a robust investment trend, as over 50% of manufacturers plan to adopt AI by 2025.
The focus is clear: enhancing operational efficiency and production flexibility. And let’s not forget the robotics side of things. The industrial robotics market is expected to grow from $50.3 billion in 2021 to $86.6 billion by 2027.
Future trends point towards smarter factories with collaborative robots working seamlessly with humans, boosting overall productivity. Continuous advancements will lead to predictive maintenance and smarter automation systems.
This isn’t just about keeping up; it’s about leading with innovation and embracing a future where technology drives unparalleled efficiency and growth.
Frequently Asked Questions
How Does AI Increase Efficiency in Manufacturing?
AI increases manufacturing efficiency through predictive maintenance, quality control, and process optimization. Utilizing data analytics, it enhances supply chain management, energy management, production scheduling, defect detection, cost reduction, and fosters workforce collaboration, driving innovation and productivity.
How Do Robotics Make Manufacturing More Efficient?
Robotics enhance manufacturing efficiency through robotic assembly, precision control, and task automation. Process integration and advanced material handling accelerate production speed, while quality assurance, workforce safety, cost reduction, and optimized supply chain processes guarantee superior outcomes.
What Is the Impact of AI and Robotics on the Manufacturing Sector?
AI integration and robotics in manufacturing drive workforce transformation, enhance quality control, and enable predictive maintenance. This fosters supply chain optimization, cost reduction, and process innovation through data analytics, real-time monitoring, and human-robot collaboration.
Can Automation Increase the Efficiency of Manufacturing?
Yes, automation can markedly increase manufacturing efficiency by enabling smart factories, production optimization, workforce integration, predictive maintenance, real-time monitoring, quality control, energy management, process automation, and advanced data analytics, thereby streamlining the supply chain and enhancing overall productivity.
Conclusion
The integration of AI into robotics is revolutionizing manufacturing automation. Enhanced worker safety, cost reduction strategies, predictive maintenance, quality control innovations, and real-time optimization are transforming the industry. Future trends suggest even greater advancements, propelling efficiency to new heights. As these technologies evolve, manufacturing will continue to benefit, ushering in an era of unprecedented productivity and innovation. The potential for growth and improvement in the sector is immense, promising a bright future for industrial automation. Intelligent robotic systems are paving the way for increased flexibility and adaptability in manufacturing processes. With the continuous development of AI algorithms, these systems are becoming more adept at handling complex tasks, increasing overall productivity. As these technologies continue to mature, the potential for intelligent robotic systems to revolutionize various industries beyond manufacturing is becoming increasingly evident.